|
Research on plastic working of light-metal alloys |
An analysis for circular-cup deep drawing of aluminum alloy sheets
Innumerable problems regarding aluminum cans to solve
Aluminum cans, which are familiar to us, are made by circular-cup deep
drawing. Seeing aluminum cans on a routine basis, we tend to think that
can manufacturing is one of mature technology. However, we still have various
technical problems, and the irregularity of edge shape along the circumferential
direction of cans, so-called "ear", is typical of them (see Fig.1).
This results from the textures of metal sheets. In general, metal sheets
have a crystal orientation distribution with a bias toward a certain direction
depending on the manufacturing process. It is known that the deep drawing
of metal sheets made through a different manufacturing process produces
change in the shape of ear.
Can manufacturers mount can lid components after removing the ears.
Therefore, in order to avoid an increase in the production cost due to
low yields and implement environmental protection measures such as the
energy saving, materials without causing ears during the process are required.
A moving image of circular-cup deep drawing→
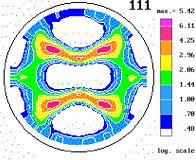
Fig.1 A deep-drawn cup with four ears Fig.2 The texture of a material
with four ears
(111 pole figure)
A contribution to society that simulation techniques can give
The objective of our study is to develop a computer software that can
predict the actual shape of ears formed during deep drawing using material
data obtained from a metal sheet (Fig.2). This software enables us to predict
the shape of ears without experiments and propose a guideline for developing
materials that form no ears in the future. Since these are quite effective
in the reduction of production costs and environmental measures, a contribution
to society directly connected with environmental issues can be made by
simulation technique.
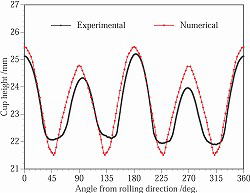
Fig.3 The shape of deformation for a quarter region Fig.4 A comparison
of the shape of ear
|
Formability of magnesium alloy rolled sheets
Magnesium is the lightest in the practical metals, and its specific
gravity is approximately two-thirds of that of aluminum and one-fourth
of that of iron. Moreover, magnesium has a high strength per weight, i.e.,
specific strength and excellent recyclability, being now in increasing
demand as an environmentally friendly material.
However, magnesium alloys have poor plastic formability at room temperature,
and it has not yet been in the actual use to form magnesium alloys by cold
press, which has good productivity. Considering this circumstance, we conduct
numerical simulation and some experiments to show an index for making magnesium
alloys with good formability.
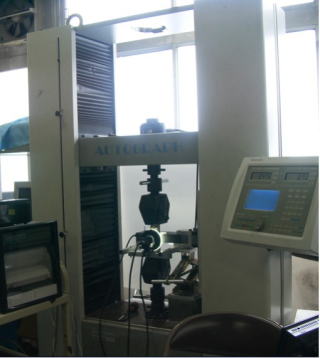
Modeling of materials
It is important for numerical simulation how to construct material models
that can express the deformation behavior of materials with high accuracy.
For this reason, material properties are investigated through experiments
or literature, being formulated and incorporated into simulation programs.
Once the material models are constructed, it is possible to perform numerical
experiments, or simulation with computers.
Fig.5 A tensile test
Numerical simulation
Modeling the texture inside the material, we discuss what texture should
be made to improve the formability of magnesium alloys. It is observed
that a change in the texture inside the material improves the formability,
as shown in the figure below.
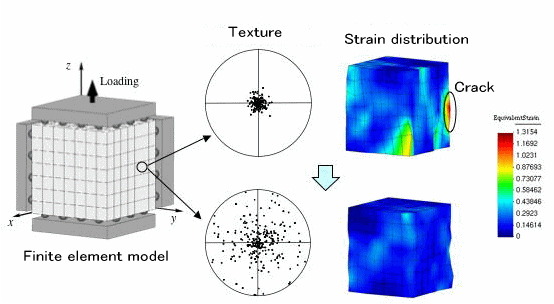
Fig.6 The effect of the textures inside a material on the strain distributions
|
|
|